Замена гальванического хрома на экологически чистый процесс напыления твердосплавных покрытий. Гальванический хром
Гальваническое оборудование для хромирования
Электрохимическое хромирование – насаждение на поверхности деталей слоя хрома определенной толщины под воздействием электрического тока. Технология используется для увеличения износостойкости поверхностей, восстановления их первоначальных размеров, антикоррозионной защиты и в декоративных целях. Главный элемент линий – гальванические ванны. Наша компания изготавливает продукцию согласно действующему ГОСТу 23738-85. В зависимости от технологических особенностей производства ванны для хромирования могут иметь несколько видов.

Ванны без кармана
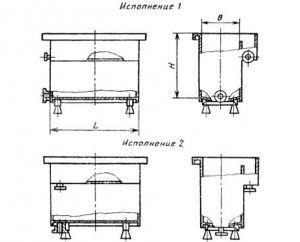
Ванны с карманом
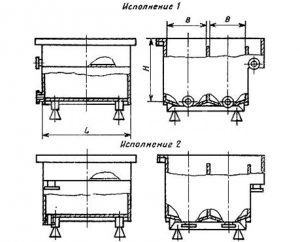
Ванны с двухступенчатой промывкой
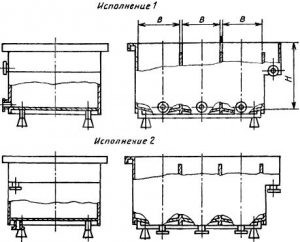
Ванны с трехступенчатой промывкой
В зависимости от типа линии оборудование для хромирования включает в себя набор дополнительных агрегатов и установок. Хромирование может выполняться на:
- Линиях с ручным управлением. Управление технологическим процессом осуществляется оператором при помощи пульта. Метод применяется при штучном или мелкосерийном производстве.
- Линиях с полуавтоматическим управлением. Вручную задается лишь номер позиции.
- Автоматических линиях. Применяется на крупносерийном производстве. Оборудование для хромирования управляется специальной компьютерной программой.
Выпускаемые нами гальванические ванны можно устанавливать на любые типы линий, на них есть возможность монтировать все необходимое дополнительное технологическое оборудование.
Для обеспечения безопасности процесса в оборудование для хромирования включаются следующие специальные агрегаты:
- Общецеховая или общезаводская химически устойчивая вентиляция. Отдельно монтируются вытяжные зонты и бортовые отсосы.
- Оборудование для подготовки деталей. Имеют вид барабанов, используются для предварительной подготовки деталей.
- Запорная водопроводная арматура и трубопроводы из химически устойчивых материалов.
- Системы автоматики. Дозаторы, контроллеры потока и т. д.
- Выпрямители постоянного тока, регуляторы напряжения и силы, нагревательные элементы, предохранительная электрическая арматура. Выбирает оптимальные режимы для хромирования различных изделий с учетом заданных оператором параметров.
- Емкости для очистки технологических вод, фильтровальные установки, накопители отходов.
- Электрические шкафы управления.
В зависимости от пожеланий заказчика перечень агрегатов на линиях может корректироваться.
Особенности подготовки ванны для хромирования
Хромирование деталей происходит в емкостях в среде химического раствора серной кислоты (в пределах 0,8–1,2%) и хромового ангидрида. Раствор приготавливается в запасной ванне из химически инертных пластиков. В емкость наливается половина объема деминерализованной воды и порционно добавляется хромовый ангидрид при постоянном перемешивании до полного растворения. Порошок хромового ангидрида должен соответствовать стандарту ВN-76/6068-11 и иметь в своем составе не более 0,4% серной кислоты. Химическая металлизация выполняется одним из четырех сортов хромового ангидрида: S, I, II и III. В зависимости от сорта изменяется процент серной кислоты. Недостающее количество кислоты добавляется только после проверки плотности жидкости ареометром. Содержание хромового ангидрида определяется по Табл. №1.
Табл. №1. Плотность водного раствора хромого ангидрида при t° = +15°С
Электрохимическое хромирование – непрерывный технологический процесс, параметры покрытия зависят от температуры, плотности раствора и силы тока. В целях экономии энергоносителей современные технологии используют универсальные растворы, что дает возможность регулировать толщину слоя хрома только за счет температуры и времени выдержки. При этом плотность тока не превышает 15–20 А/дм2, а температура +40–50°С. Металл подается в ванную подогретым до рабочей температуры.
Табл. №2. Зависимость толщины покрытия от времени процесса и плотности тока, t° +40°С
Табл. №3. Зависимость толщины покрытия от времени процесса и плотности тока, t°+55°С
Гальваническое хромирование должно выполняться при правильном пространственном положении внутреннего анода и матриц. Если изделия располагаются неправильно, то выделяющиеся на поверхности пузырьки газов препятствуют равномерному осаждению хрома. На рис. 1 показано правильное положение, а на Рис. 2 неправильное.

Правильное размещение изделия

Неправильное положение изделий
1 – анод;
2 – изоляция анода;
3 – зеркало раствора;
4 – изоляция изделия;
5 – покрытие хромом.
Виды покрытий
Процесс гальванического хромирования корректируется с учетом требуемых видов поверхности деталей.
- Двухслойные покрытия комбинированного типа. Придают хрому повышенную износостойкость, увеличивают размеры изделий. Применяется комбинация износостойкого и непористого молочного хрома. Хромирование делается в два этапа. Первый этап протекает при плотности тока 30 А/дм2 и температуре 343 К (+70°С), наносится молочный хром толщиной в пределах 9 мкм. Второй этап – температура раствора понижается до 328 К (+55°С), а катодная плотность тока увеличивается до 45–55 А/дм2. Длительность завершающего процесса устанавливается в зависимости от желаемой толщины слоя хрома.
- Черные покрытия. Для нанесения используется то же оборудование для хромирования, меняются только режимы нанесения. Имеет небольшую толщину (в пределах 1,5–2,0 мкм), характеризуется высокой теплопроводностью и адгезией к основанию. Металл сохраняет первоначальные физические свойства при температурах до 773 К (+500°С).
- Пористые покрытия. К ним не относятся молочные, хромирование специально делается таким способом, чтобы на поверхности появлялись микроскопические поры. В них в дальнейшем удерживаются смазочные материалы, что уменьшает износ трущихся поверхностей. Электрохимическое хромирование для пористого покрытия продолжается 10–12 минут при катодной плотности тока 40–60 А/дм2 и температуре раствора 325 К (+50°С) – 331 (+57°С) К.
Качество покрытия во многом зависит и правильности выбора режимов и тщательности предварительной подготовки изделий. Они должны быть очищенными от загрязнений и масляных пятен, острые углы и необрабатываемые отверстия закрытыми. Оборудование для хромирования настраивается технологом, контроль за соблюдением процессов производит оператор. Существующие нормативные документы устанавливают следующие требования по технологическом процессу:
- Допускается кратковременное изменение температуры раствора в пределах ±10°С. Если электролит охладился или перегрелся выше указанных полей допусков, то процесс считается прерванным. Дальнейшие действия зависят от степени нарушения качества покрывающего слоя. После анализа состояния поверхностного слоя хромирование может продолжаться или прекращаться, решение принимает технолог производства.
- Подвески и контакты должны изготавливаться из аналогичного материала. Остальное оборудование не должно подвергаться воздействию агрессивных химических соединений.
- Поперечное сечение всех токопроводящих элементов должны выдерживать требуемые значения с запасом. Величина запаса подбирается с учетом сортамента обрабатываемой продукции. Химическая металлизация выполняется одновременно с максимально широким ассортиментом. Перестраивать и переналаживать гальванические ванны для хромирования под каждый тип изделий экономически невыгодно. Надежность контактов должно обеспечивать длительную работу без появления окалины и перегрева, любые скачки величины тока оказывают негативное влияние на качество прокрывающего слоя.
- Специальное оборудование для подвески должно обеспечивать одинаковое расстояние между однотипными деталями, в противном случае показатели покрывающего слоя не будут идентичными. На поверхности одних появится «пригар», на других образуется матовый оттенок.
- Категорически запрещается прерывание тока во время процесса. Гальваническое хромирование от начала и до конца должно выполняться в указанных режимах. При повторном включении новое покрытие отслаивается от старого, детали подлежат выбраковке и повторной обработке. Допускается повторное покрытие хромом только после анодного травления, при этом хромирование начинается с минимальных значений тока.
- Детали со сложным рельефом поверхности нужно хромировать после «скачка тока». Показатели тока на 1–2 минуты увеличивают в два раза против расчетных, в дальнейшем ток понижают и продолжают процесс. За счет такой технологии слой хрома осаждается в самых углубленных местах.
Некачественное гальваническое хромирование деталей из сплавов меди и стали может сниматься раствором соляной кислоты в пропорции 1:1. На изделиях, насыщение которых водородом не допускается, некачественный слой снимается в щелочных растворах.
Основные дефекты и их причины
Вид дефекта | Причина |
Покрытие отслаивается от поверхности | Некачественно очищены поверхности, резко понизилась температура, несоответствие величины тока. |
Хром отслаивается вместе с подслоем никеля | Пониженное значение pH электролита. |
Внешний вид покрытия имеет серый оттенок | В растворе недостаточно серной кислоты. |
Пропуски или неравномерность покрытия по толщине | Плохая подготовка поверхностей, экранирование близкорасположенных элементов на подвесках. |
Большое количество точеных углублений | Неправильное расположение деталей по отношению к электроду. |
При необходимости сотрудники нашей компании окажут теоретические консультации по выбору оптимальных размеров ванн и технологий хромирования различных деталей.
plast-product.ru
Гальваническое покрытие. Технология гальванических покрытий. Гальваника
Гальванической покрытие представляет собой метод покрытия одного металла каким-то другим посредством электролиза. Эта процедура осуществляется с использованием традиционных методов погружения. После предварительной подготовки печатные платы загружают в гальваническую ванну, представляющую собой емкость из диэлектрика, которая наполнена электролитом и снабжена анодами (они могут быть растворимыми и нерастворимыми), а также устройством для поддержания температуры и перемешивания раствора.
Обработка плат
Пропускание постоянного тока приводит к тому, что непокрытые защитной маской и подключенные к электроду участки платы покрываются слоем никеля или золота определенной толщины. Правильное расположение анодов гарантирует, что толщина покрытия будет примерно равномерной.
Золочение печатных плат обычно производится с использованием двухстадийного процесса. Сначала их погружают в ванну, где гальваническим способом наносится никель. При этом используется высокая плотность тока, благодаря которой из кислого раствора осаждается слой никеля, толщина которого составляет 0,05-0,1 мкм. Благодаря этому обеспечивается прочное сцепление никеля и меди, что позволяет уменьшить пористость покрытия, а также предотвратить проникновения меди в золотой слой. После промывки изделия обычно перемещают в ванну золочения, где производится наращивание слоя золота до 0,5 мкм из электролита.
Гальваника и декорирование
Уже в древние времена существовала декоративная отделка художественных металлов. Современное производство предполагает, что для придания каких-то особых свойств поверхности металла будет использоваться гальваническая обработка. Защитные покрытия из благородных металлов можно получить благодаря осаждению металлов из солевых растворов под действием электрического тока. Благодаря таким покрытиям удается достаточно длительное время сохранить цвет и блеск ювелирных изделий. Они не только предотвращают потемнение изделий, но и обладают превосходным полирующим эффектом. К примеру, гальваническое покрытие золотом или серебром позволяет надолго сохранить цвет и блеск ювелирного изделия.
Существует несколько разных вариантов этого процесса, каждый из которых предполагает использование того или иного металла:
- хромирование;
- меднение;
- цинкование;
- никелирование;
- олово-висмутовое покрытие;
- химическое оксидирование;
- химическое пассивирование;
- анодирование;
- электрополировка.
Хромирование
Это диффузное насыщение стальной поверхности хромом либо осаждение на детали слоя вещества из электролита под действием электротока. В данном случае гальваника ориентирована на защиту от коррозии, применяется для декорирования либо для увеличения степени твердости поверхности. Хромирование в промышленности может использоваться и для декорирования. В данном случае основная цель процедуры – придание металлической поверхности красивого эффектного блеска. Деталь перед нанесением хрома должна быть отполирована.
Свойства покрытия
Твердое хромовое покрытие характеризуется жаростойкостью, высокой степенью износостойкости, плохой смачиваемостью, низким коэффициентом трения, а также незначительной пластичностью. Кроме того, поверхность получает такие свойства, как устойчивость в плане трения, способность выдерживать распределительную нагрузку, а также недостатком, связанным с легкостью разрушения под действием сосредоточенных ударных нагрузок. Гальваническое покрытие в форме молочного хрома обладает невысокой степенью износостойкости и твердости, малой пористостью. Поверхность получает защиту от коррозии, при этом сохраняя привлекательный декоративный вид.
Использование хромирования в промышленности
Основная цель, с которой оно используется в промышленности, это придание детали таких свойств, как повышенная износостойкость, увеличенная устойчивость к коррозии, а также сниженное трение. Благодаря этому процессу сталь становится прочнее, не подвергается газовой коррозии, а также не разрушается в морской и обычной воде, азотной кислоте. Гальваническое покрытие данного типа приводит к тому, что поверхностные дефекты становятся только значительнее, из-за чего требуется производить последующую обработку, так как в данном случае нет эффекта выравнивания.
Меднение
Использование медных покрытий актуально в тех случаях, когда требуется повысить электропроводность, а также их применяют в качестве промежуточного слоя на стальных изделиях перед тем, как будет нанесено хромовое, никелевое или иное покрытие. Так удается обеспечить более качественное сцепление, а также повысить защитную способность. Гальваническое покрытие медью обычно не используется в качестве самостоятельного или декоративного. Благодаря тому, что данный металл способен предотвращать образование искр, изделие можно использовать в нефтяной и газовой промышленности.
Применение меднения
Данный процесс используется для нанесения покрытия из меди на стальные изделия либо на стальную проволоку. Часто этот вид покрытия применяется для защиты отдельных участков изделий из стали от цемента, а обработке при этом подвергаются те участки, которые дальше предполагается обрабатывать резанием.
Гальванические покрытия металлов в данном случае часто применяются в нефтегазовой отрасли, чтобы исключить образование искр, в электроэнергетической сфере для последующего нанесения многослойных покрытий, предназначенных для защиты и декорирования, в производстве печатных плат, для улучшения пайки, а также для многого другого. Поверхность приобретает цвет от светло-розового до темно-красного. Оттенки обычно не нормируются.
Цинкование
Одним из наиболее распространенных методов для защиты металлических изделий является цинкование. Обычно его применяют для обработки разнообразных легированных или углеродистых марок стали. Нанесение гальванических покрытий данного типа достаточно востребовано для защиты изделий из проволоки и крепежных элементов. Попадая во влажную среду, цинковая поверхность выступает в качестве анода, благодаря чему замедляются окислительные реакции, а основной металл при этом получает надежную защиту от негативных факторов среды.
Гальваника данного типа может использоваться только после того, как металлических изделия будут обработаны особым образом. Для этого следует очистить их от ржавчины, окалины, технических средств смазочно-охлаждающего назначения. Когда процесс гальванического цинкования будет завершен, изделие должно подвергнуться осветлению, то есть его протравливают слабым раствором азотной кислоты, после чего проводят пассивацию. Так не только удается увеличить устойчивость оцинкованных изделий к негативным факторам, но и сделать их более декоративными, то есть придать блеск и определенный оттенок. Технология гальванических покрытий в данном случае предполагает толщину цинкового слоя от 6 мкм до 1,5 мм.
Никелирование
Защита металлических изделий может осуществляться с использованием различных технологий. Одной из наиболее востребованных и распространенных на данный момент является никелирование. Такая популярность объясняется химическими свойствами никеля. Он обладает высокой степенью устойчивости к коррозии в водной среде, а оксид никеля предотвращает последующее окисление металла. Помимо этого, никель слабо поддается воздействию солей, кислот и щелочей, за исключением азотной кислоты. К примеру, гальваническое покрытие толщиной 0,125 мм надежно защищает от большинства промышленных газов, характеризующихся повышенной агрессивностью. Очень важен и такой момент: никелированию поддаются почти все металлы, благодаря чему такой способ можно применять для дополнительной обработки изделий.
Использование никелирования уместно для решения целого ряда задач:
- обеспечение защиты металлических изделий;
- использование в качестве декоративного покрытия;
- формирование предварительного слоя, который будет подвергнут дальнейшей обработке;
- восстановление деталей и узлов.
Покрытие характеризуется повышенной износостойкостью и твердостью и рекомендовано для деталей, которые работают в условиях трения, в особенности при отсутствии какой-либо смазки, используется для защиты от коррозии, а также обеспечения качественной пайки низкотемпературных припоев, все это прописано в ГОСТ. Гальванические покрытия обладают повышенной хрупкостью, поэтому не рекомендовано производить развальцовку и гибку деталей, прошедших процедуру никелирования. Его рекомендуется применять для сложнопрофилированных деталей. После процедуры термообработки в условиях температуры 400 градусов Цельсия покрытие приобретает максимальную твердость.
Олово-Висмут
Оловянное покрытие характеризуется стойкостью к действию соединений, содержащих серу, поэтому рекомендуется для деталей, которые находятся в контакте с резиной и пластмассами. Среди его свойств можно назвать превосходное сцепление с основным металлом, эластичность, способность к изгибу, вытяжке, штамповке, развальцовке, прессовой посадке, а также хорошее сохранение при свинчивании. Свежеосажденное оловянное покрытие хорошо поддается пайке.
Выводы
Гальваническое покрытие позволяет улучшить токопроводящие характеристики деталей, придавая им превосходные свойства электроизоляции, а также защищая от воздействия различных веществ. Кроме того, этот способ позволяет получить отличные поверхности, имеющие зеркальный вид, а также имитирующие покрытие эмалью. Сложно переоценить, насколько гальваника важна в современном производстве, так как развитие технологий позволило сделать процесс более совершенным.
fb.ru
гальваническое, диффузионное и другие технологии
Нанесение на поверхность автомобильных дисков защитного слоя позволяет не только повысить привлекательность товара для покупателей, но и увеличивает срок их службы. Хромирование дисков создаёт им прекрасную защиту от влияния внешних факторов.

Хромирование дисков
Воздействие вредоносных факторов на диски колёс автомобиля при движении по дорогам требует их защиты от коррозии. К ним относят присутствие:
- влаги;
- солей;
- других агрессивных компонентов.
Защита от них предусматривает:
- покраску;
- нанесение покрытий типа:
- хромирования;
- жидкого стекла;
- нанокерамики.
Хромирование дисков позволяет предохранить их от влияния агрессивной среды, обеспечить дополнительную привлекательность автомобилю. Нанесение хромового покрытия означает насыщение хромом поверхности колесных дисков.
Хромирование автомобильных дисков обеспечивает антикоррозионную защиту, отсутствие повреждений при механическом воздействии (сколы, царапины).
Технологии нанесения хрома
Различают следующие технологии хромирования:
- гальванический;
- диффузионный;
- горячий;
- вакуумный;
- химический;
- покраска хромсодержащими красками.
При любой технологии хромирования дисков обязательно проводится очистка их от грязи, масел, коррозии, других посторонних загрязнений с последующим обезжириванием. Это обеспечивает получение защитной плёнки из хрома надлежащего качества.
Различают промышленный и индивидуальный метод получения хромового покрытия. Только в промышленных условиях можно обеспечить необходимые параметры процессов хромирования при гальваническом, горячем, вакуумном способах хромирования с соблюдением гигиенических норм.
Гальваническое хромирование дисков
Процесс гальванического хромирования литых дисков является дорогостоящей и продолжительной по времени технологической операцией. Он основан на протекании электрохимических реакций, которые приводят к адгезии хрома в подложку (диск колеса).

Гальваническое хромирование дисков
Электрохимическая реакция происходит в электролите с погружённым диском. Чтобы шла эта реакция нужно иметь большую ёмкость. Для запуска электрохимической реакции необходимо подключение электрического тока к электродам, которые погружены в электролит. Катодом является автомобильный диск, анодом — деталь, содержащая хром. Хром осаждается на катоде.
Хромирование литых дисков производят в автоматическом или полуавтоматическом режимах, что обеспечивает минимальное соприкосновение человека с химическими веществами и выбросами, возникающими при проведении обработки (пары и вредные испарения).
После хромирования их извлекают из ванны и промывают в дистиллированной воде, а после просушки — полируют до получения блеска.
Для получения требуемых параметров получаемого покрытия подбирают нужную силу тока (до 50 А) и вид электролита. Нужно также учитывать марку металла, из которого изготовлен диск. При необходимости можно нанести несколько покрытий, каждый из которых отличается по внешнему виду, защитным свойствам.
Диффузионный и горячий способы
При диффузионном хромировании штампованных дисков насыщение их поверхностного слоя молекулами хрома происходит в печи при высокой температуре. Это становится возможным за счёт обеспечения парообразного состояния содержащих хром заготовок при нагреве.
При горячем хромировании сварных дисков их погружают в ванну с расплавленным хромом. Это позволяет создавать слой хрома на изделиях.
Хромирование в вакууме
Вакуумное хромирование колёсных дисков предполагает использование оборудования, обеспечивающего проведение этого процесса в вакууме. Камера вакуумной установки вмещает их и заготовку из хрома, которую разогревают до 600°С. При воздействии вакуума и температуры происходит перенос хрома на поверхность диска.
Задавая параметры вакуума, температуры нагрева можно регулировать характеристики хромирования: толщину, плотность покрытия, скорость его нанесения.
Существует несколько способов вакуумного нанесения покрытий, что подразумевает разную конструкцию применяемых установок.
Наличие вакуума позволяет получить качество покрытия лучше, нежели при использовании гальванического метода. Однако стоимость этого напыления гораздо выше, чем полученная гальваникой.
Покраска
Для придания защитных свойств поверхности производится декоративное хромирование штампованных дисков с использованием лакокрасочных покрытий, содержащих хром. Это один из наиболее доступных способов получения защитных покрытий. Используются однокомпонентные и двухкомпонентные краски.
Однокомпонентные краски распыляют из аэрозольного баллона. Краски из двух компонентов продают в банках. Их наносят на автомобильные диски при помощи кисти.
Покрытие, полученное при использовании двухкомпонентной краски, более износостойкое. Лучшие показатели получают при нанесении грунтовки перед покраской.
При хромировании железных дисков краской получают толщину покрытия большую, чем у перечисленных выше методов. Но оно менее износостойкое и служит не более двух лет, после чего его нужно возобновлять.
Химический метод
При данном методе осаждения хрома в качестве электролита используют дистиллированную воду, используемую для растворения реагента с содержанием хрома. Химическая реакция возникает при погружении диска в раствор с растворённым реагентом. Её результатом является осаждение хрома на нём.

Результат химического хромирования дисков
Этим методом можно осуществлять химическое хромирование дисков в гараже при соблюдении необходимых мер предосторожности. Необходимым условием при проведении этого процесса должна быть обеспечена хорошая вентиляция помещения. Кроме этого нужно использовать респиратор, перчатки, другие элементы защиты человека от агрессивных веществ.
Надёжность этого покрытия ниже, чем полученного гальваникой. Его можно использовать для хромирования штампованных дисков своими руками. Затраты на получение такого покрытия ниже, чем при гальваническом методе.
Уход за дисками
Для сохранения надлежащего качества поверхности хромированных дисков нужно выполнять несложные требования:
- Мыть и чистить их поверхность водой с использованием мягкой ткани. Окончательную промывку совершают с использованием большого количества воды. Эту операцию желательно совершать два раза в месяц. После сушки желательно провести полировку покрытия для придания ему зеркального блеска.
- Для зачистки мелких дефектов на покрытии используют измельчённый до пыли мел и салфетки. Затем обработанные дефекты покрывают бесцветным лаком, который сохраняет оксидную плёнку и препятствует дальнейшему разрушению покрытия.
- Для промывки хромовых покрытий нужно использовать тёплую воду. Если на покрытии появилась засохшая грязь, то её нужно сначала размочить. Только после этого её можно удалять мягкой тканью. Появляющийся на покрытии налёт нужно удалять мягкой губкой.
Преимущества и недостатки хромирования
Преимущества хромированных дисков, по сравнению с покрашенными, заключается в следующем:
- увеличение эксплуатационных характеристик за счёт улучшения теплообменных свойств после хромирования;
- повышение твёрдости, прочности поверхностного слоя диска позволяет избежать царапин, сколов при их эксплуатации;
- повышенная коррозионная стойкость при агрессивном воздействии воды, грязи, химических соединений присутствующих на дороге.

Автомобильный диск до и после хромирования
К недостаткам гальванической, химической технологий нанесения покрытий из хрома можно отнести токсичность электролитов и паров, возникающих при хромировании. Это отрицательно сказывается на здоровье человека. Поэтому лучше их проводить в промышленных условиях с обеспечением всех санитарных норм.
Если вы нашли ошибку, пожалуйста, выделите фрагмент текста и нажмите Ctrl+Enter.
stankiexpert.ru
Какое оборудование для хромирования бывает?
Хромирование различных металлических поверхностей стало самым распространенным способом защиты металлов от коррозии. Оборудование для этих целей бывает разное, и в настоящее время выделяют несколько способов хромирования, при этом нередко бытует мнение, будто все они настолько просты, что выполнять работы по хромированию можно едва ли не в условиях жилого помещения.
1 Принцип работы хромирующей установки
Достаточно лишь приобрести оборудование для хромирования, и можно приступать к работе. Но все это далеко не так просто. Хотя удобная действительно существует негабаритная установка для хромирования. Выпущена она была в США не так давно и состоит из стенда, набора манометров, пистолета обдува и пульверизатора. Прилагается и инструкция по пользованию. Но стоит такое устройство прилично: около 2000 долларов. Более дешевый аппарат был выпущен и в России. Казалось бы, вот оно решение в вопросе защиты деталей автомобиля или иных металлических поверхностей! Но в названии устройства умышленно опущено ключевое слово «декоративное». Именно для подделки под хромирование и предназначено это оборудование.

Оборудование для хромирования
Рекомендуем ознакомиться
Принцип работы прост. Сначала готовится поверхность: ее зачищают от защитного слоя краски, шлифуют, обезжиривают и покрывают слоем надежной грунтовки. Желательно подвергнуть ее тепловой обработке, чтобы грунт получил более надежное сцепление с поверхностью. На остывшую деталь напыляется слой хрома. Люди, которые пользовались устройством для хромирования деталей, утверждают, что потребуется еще дополнительная защита в виде слоя лака или нанесения самоклеящейся пленки. Как мы все понимаем, такое «хромирование» не создаст барьера для коррозии.

Нанесение покрытия
В действительности под хромированием следует понимать химическую или электрохимическую реакцию металла и реагентов, в результате которого на поверхности образуется тонкий защитный слой (в данном случае слой хрома).
2 Настоящее и псевдо хромирование
Самый простой метод холодного хромирования тоже нельзя отнести к настоящему способу нанесения покрытия. Заключается он в том, что использоваться будет краска, в состав которой введено не менее 75% пыли хрома. Краска наносится на поверхность с помощью пульверизатора (в некоторых случаях можно использовать обычные малярные кисти), застывает и создается своеобразный буфер для коррозии. Служит такая защита не менее 5 лет. Но стоит только немного повредить покрытие, как «жучок» проникнет под слой защиты и начинает свою работу.

Покраска хромом
Настоящее хромирование подразумевает наличие следующих составляющих:
- гальваническая ванна;
- электролит;
- источник постоянного тока.

Гальваническое покрытие
И это минимум, необходимый для правильного протекания всех химических процессов.
3 Как выполняется промышленное хромирование?
Деталь, которую вы собираетесь хромировать, помещается в ванну, заполненную электролитом. К ней подключается положительный провод от источника тока. К отрицательному полюсу подключается любая заготовка из хрома. После подачи тока будет происходить следующее: за счет диффузии от заготовки будут отделяться ионы цинка. Они являются носителями тока, поэтому через жидкую среду начнется движение в сторону детали. Ионы будут оседать на поверхности, создавая защитный слой. Будет ли он надежным? А как вы считаете, если связь металла детали и слоя хрома будет обеспечена на ионном уровне? Это и есть настоящее хромирование и самая долговечная защита поверхности.

Ванна с электролитом
Гальванические ванны могут быть использованы и для нанесения защиты иными металлами: серебром, алюминием, цинком. Такой способ еще называется методом химической металлизации. В домашних условиях процесс хромирования проводить не стоит: слишком высокое выделение побочных продуктов химических реакций. А вот в условиях гаража и при наличии средств индивидуальной защиты этот процесс можно осуществить. Правда, с токами придется немного повозиться, чтобы добиться равномерной скорости прохождения реакции.
Химическое хромирование не подразумевает наличие источника тока, поскольку здесь на поверхность металла наносится несколько реагентов.

Химическое хромирование
Химическая реакция, которая протекает на металле, оставляет после себя налет хрома (или цинка, зависит от реагентов). Держится такая защита тоже очень долго.
4 Термохимическая металлизация
Интересно протекает термохимическое нанесение металла на поверхность. Напоминает оно в точности процедуру, которую в былые годы использовали для золочения поверхностей. В недалеком прошлом любая металлизация проводилась именно так. Сначала на поверхность наносится слой смеси металла и связывающего вещества (на основе древесных смол). Составу дают время высохнуть, и после этого изделие помещают в муфельную печь. От высокой температуры связующее вещество выгорает, а металлическая пыль плавится, растекаясь по поверхности и создавая слой защиты.
В настоящий момент такая металлизация поверхностей более усовершенствована: в тепловую печь помещается изделие, и под высоким давлением на него напыляется все тот же хром. Существует вариант первоначального напыления с последующим обжигом. Так получается быстрее и качественнее. В домашних условиях процесс такого метода хромирования значительно упрощен. Сначала поверхность покрывается тонким слоем металлической пыли, которая впоследствии плавится при нагревании феном. Здесь есть один нюанс: слой защиты не всегда получается ровным, периодически могут возникать потеки металла. Устраняется этот недостаток за счет последующей шлифовки и полировки поверхности.

Печь для термохимической металлизации
Методом напыления хрома пользуются очень многие мастера, так как для этих целей нужен небольшой набор инструментов:
- пульверизатор;
- фен;
- шлифовальная машинка;
- полироль.
Но не стоит забывать, что распыление металлических квасцов тоже сопряжено с риском для здоровья. Не забывайте защитить свои органы дыхания и глаза.

Метод напыления хрома
Горячее хромирование металлических деталей
Самый сложный способ хромирования - горячий. Применяется он в промышленном производстве, где затраты на энергоносители перекрываются за счет большого количества хромируемых деталей.
Простота такого метода очевидна: в ванну с расплавленным хромом опускается деталь, которая затем поднимается и вращается до тех пор, пока слой хрома не застынет на поверхности. Осуществить такое хромирование в домашних условиях не представляется возможным.
5 Выводы по теме публикации
Какой бы вы способ хромирования ни выбрали, имейте в виду, что все химические реакции сопровождаются большим количеством побочных продуктов, наносящих вред всему живому. Если процесс будет проводиться в гаражных условиях, то скоро вы заметите, как быстро возле рабочего места исчезнет вся растительность.

Хромирование в гаражных условиях
Для вашего организма работы по хромированию тоже не проходят бесследно. Если у вас нет уверенности в собственных умениях и знаниях в области химии и физики, то браться за такую работу не стоит. Доверьте это людям, которые имеют в наличии все необходимые инструменты и опыт выполнения работ данного вида. Это будет безопасно для здоровья и пусть немного «ударит» по кошельку, зато вы будете уверены в качестве нанесенного покрытия.
tutmet.ru
Замена гальванического хрома на экологически чистый процесс напыления твердосплавных покрытий.
Технологии высокоскоростного газопламенного и плазменного напыления позволяют наносить твердосплавные покрытия, которые превосходят гальванический хром по всем параметрам, и при этом не являются канцерогенными, не вредят окружающей среде. Напыление металлокерамических покрытий позволяет повысить качество и продолжительность работы штоков гидравлики, плунжеров, валов каландров, шаров и шиберов запорной арматуры и пр.
Гальваническое хромирование долгое время считалось естественным выбором, когда необходимо было обеспечить высокие износо- и коррозионную стойкость поверхности изделия. Хромовые покрытия, при небольшой толщине, обладают твердостью более 60 HRC, адгезией более 30 МПа, противостоят многим агрессивным средам и благодаря своей высокой плотности надежно защищают поверхность от коррозии. Высокая экономическая эффективность нанесения на большие партии одинаковых изделий позволяла забыть про такие недостатки, как склонность к наводораживанию, сложность защиты нехромируемых зон и продолжительность процесса нанесения покрытий с толщиной более нескольких микрон.
Повышенная смертность от рака рабочих гальванических производств, а так же людей, живущих поблизости, заставила медиков провести в 70-80-е годы ХХ века множество исследований, которые показали однозначную причинно-следственную связь между гальваникой и развитием раковых клеток. Основным канцерогеном оказался шестивалентный хром, образующийся в ходе процесса хромового покрытия. Это открытие, признанное и в странах большой семерки, и в СССР, привело к различным результатам. Все развитые страны, включая СССР, ужесточили экологическое регулирование гальванических процессов. При этом США, Евросоюз и Япония приступили к поиску и стимулированию экономически эффективных альтернатив хромированию, Россия же оставила предприятия один на один с проблемой канцерогенного производства и инспекторами природнадзора.
В условиях перехода от крупносерийного к средне- и мелкосерийному производству наилучшей альтернативой гальванике были признаны высокоскоростное газопламенное и плазменное напыление твердосплавных покрытий из карбидов вольфрама и хрома. Эти материалы обладают более высокой твердостью (более 70HRC), адгезией (более 80 МПа), могут эффективно наноситься толщинами до 500-1000 мкм, обладают химической стойкостью в более широком спектре агрессивных сред, не приводят к наводораживанию металла, могут наноситься на заданные участки поверхности. Кроме того, с помощью газотермического напыления можно наносить защитные покрытия на такие материалы, как титан, диэлектрики. К недостаткам данных покрытий можно отнести невозможность нанесения в отверстия размером менее 150 мкм и необходимость последующей механической обработки твердых покрытий шлифованием.
Благодаря перечисленным преимуществам, а так же существенной государственной поддержке, страны большой семерки не только перевели более 70% объема деталей, ранее защищавшихся с помощью хромирования, на напыление твердосплавных покрытий, но и ужесточили в начале 2000-х годов требования к гальваническим производствам еще раз. Сегодня европейские и американские требования к экологической чистоте в гальваническом производстве существенно превышают аналогичные требования в России, что положительно влияет на снижение уровня заболевания раком в районах, где расположены такие производства.
По опыту Европы и США, газотермическое напыление успешно заменяет гальванику в производстве шаров, клинов и шиберов запорной арматуры, штоков гидравлических приводов, штоков компрессоров, плунжеров, каландровых и гладильных валов, валов целлюлозно-бумажных производств и пр.
В России работает несколько центров, предлагающих нанесение покрытий с помощью газотермического напыления. За годы работы нами поставлены десятки установок газотермического напыления под ключ, обучены сотни специалистов.
www.plackart.com
HVOF и гальваническое хромирование
Технологии высокоскоростного газопламенного и плазменного напыления позволяют наносить твердосплавные покрытия, которые превосходят гальванический хром по всем параметрам, и при этом не являются канцерогенными, не вредят окружающей среде. Напыление металлокерамических покрытий позволяет повысить качество и продолжительность работы штоков гидравлики, плунжеров, валов каландров, шаров и шиберов запорной арматуры и пр.
Гальваническое хромирование долгое время считалось естественным выбором, когда необходимо было обеспечить высокие износо- и коррозионную стойкость поверхности изделия. Хромовые покрытия, при небольшой толщине, обладают твердостью более 60 HRC, адгезией более 30 МПа, противостоят многим агрессивным средам и благодаря своей высокой плотности надежно защищают поверхность от коррозии. Высокая экономическая эффективность нанесения на большие партии одинаковых изделий позволяла забыть про такие недостатки, как склонность к наводораживанию, сложность защиты нехромируемых зон и продолжительность процесса нанесения покрытий с толщиной более нескольких микрон.
Повышенная смертность от рака рабочих гальванических производств, а так же людей, живущих поблизости, заставила медиков провести в 70-80-е годы ХХ века множество исследований, которые показали однозначную причинно-следственную связь между гальваникой и развитием раковых клеток. Основным канцерогеном оказался шестивалентный хром, образующийся в ходе процесса хромового покрытия. Это открытие, признанное и в странах большой семерки, и в СССР, привело к различным результатам. Все развитые страны, включая СССР, ужесточили экологическое регулирование гальванических процессов. При этом США, Евросоюз и Япония приступили к поиску и стимулированию экономически эффективных альтернатив хромированию, Россия же оставила предприятия один на один с проблемой канцерогенного производства и инспекторами природнадзора.
В условиях перехода от крупносерийного к средне- и мелкосерийному производству наилучшей альтернативой гальванике были признаны высокоскоростное газопламенное и плазменное напыление твердосплавных покрытий из карбидов вольфрама и хрома. Эти материалы обладают более высокой твердостью (более 70HRC), адгезией (более 80 МПа), могут эффективно наноситься толщинами до 500-1000 мкм, обладают химической стойкостью в более широком спектре агрессивных сред, не приводят к наводораживанию металла, могут наноситься на заданные участки поверхности. Кроме того, с помощью газотермического напыления можно наносить защитные покрытия на такие материалы, как титан, диэлектрики. К недостаткам данных покрытий можно отнести невозможность нанесения в отверстия размером менее 150 мкм и необходимость последующей механической обработки твердых покрытий шлифованием.
Благодаря перечисленным преимуществам, а так же существенной государственной поддержке, страны большой семерки не только перевели более 70% объема деталей, ранее защищавшихся с помощью хромирования, на напыление твердосплавных покрытий, но и ужесточили в начале 2000-х годов требования к гальваническим производствам еще раз. Сегодня европейские и американские требования к экологической чистоте в гальваническом производстве существенно превышают аналогичные требования в России, что положительно влияет на снижение уровня заболевания раком в районах, где расположены такие производства.
По опыту Европы и США, газотермическое напыление успешно заменяет гальванику в производстве шаров, клинов и шиберов запорной арматуры, штоков гидравлических приводов, штоков компрессоров, плунжеров, каландровых и гладильных валов, валов целлюлозно-бумажных производств и пр.
В России работает несколько центров, предлагающих нанесение покрытий с помощью газотермического напыления. За годы работы нами поставлены десятки установок газотермического напыления под ключ, обучены сотни специалистов.
www.plackart.com
Хром гальванические растворы - Справочник химика 21
Существуют два варианта метода определения пористости наложение на испытуемую поверхность фильтровальной бумаги, пропитанной соответствующим реактивом, и заливка этим реактивом (с добавкой желатина) испытуемого участка, трудно доступного для наложения фильтровальной бумаги. Этот метод основан на образовании в порах покрытия гальванических микроэлементов, в которых растворяющимся электродом — анодом — является основной металл или подслой. Для определения пористости покрытий медью, никелем, оловом, свинцом, хромом, нанесенных на стальную поверхность, применяют обычно раствор железосинеродистого калия, с которым ионы железа, возникающие в результате действия гальваноэлементов, образуют в порах окрашенное соединение — турнбулеву синь. По количеству синих пятен, приходящихся на единицу поверхности, судят о степени пористости покрытия. [c.447] Защитные поверхностные покрытия металлов. Они бывают металлические (покрытие цинком, оловом, свинцом, никелем, хромом и другими металлами) и неметаллические (покрытие лаком, краской, эмалью и другими веществами). Эти покрытия изолируют металл от внешней среды. Так, кровельное железо покрывают цинком, из оцинкованного железа изготовляют многие изделия бытового и промышленного значения. Слой цинка предохраняет железо от коррозии, так как цинк, хотя и является более активным металлом, чем железо (см. ряд стандартных электродных потенциалов металлов, рис. 5.5), покрыт оксидной пленкой. При повреждениях защитного слоя (царапины, пробои крыш и т. д.) в присутствии влаги возникает гальваническая пара 2п Ре. Катодом (положительным полюсом) является железо, анодом (отрицательным полюсом) — цинк (рис. 5.10). Электроны переходят от цинка к железу, где связываются молекулами кислорода, цинк растворяется, но железо остается защищенным до тех пор, пока не будет разрушен весь слой цинка, на что требуется довольно много времени. Покрытие железных изделий никелем, хромом, помимо защиты от коррозии, придает им красивый внешний вид. [c.164]Большое положительное значение перенапряжения можно показать на примере электрохимического выделения водорода. Электродные потенциалы цинка, кадмия, железа, никеля, хрома и многих других металлов в ряду напряжения имеют более отрицательную величину равновесного потенциала по сравнению с потенциалом водородного электрода. Благодаря перенапряжению водорода на указанных выше металлах при электролизе водных растворов их солей происходит перемещение водорода в ряду напряжений в область более отрицательных значений потенциала и - становится возможным выделение многих металлов на электродах совместно с водородом с большим выходом металла по току . Так, выход по току при электролизе раствора 2п504 более 95%. Это широко используется в гальванотехнике при нанесении гальванических покрытий и в электроанализе. Изменением плотности тока и материала катода можно регулировать перенапряжение водорода, а значит и восстановительный потенциал водорода и реализовать различные реакции электрохимического синтеза органических веществ (получение анилина и других продуктов восстановления из нитробензола, восстановление ацетона до спирта и др.). Перенапряжение водорода имеет большое значение для работы аккумуляторов. Рассмотрим это на примере работы свинцового аккумулятора. Электродами свинцового аккумулятора служат свинцовые пластины, покрытые с поверхности пастой. Главной составной частью пасты для положительных пластин является сурик, а для отрицательных — свинцовый порошок (смесь порошка окиси свинца и зерен металлического свинца, покрытых слоем окиси свинца). Электролитом служит 25—30% серная кислота. Суммарная реакция, идущая при зарядке и разрядке аккумуляторов, выражается уравнением [c.269]
ИЗВЛЕЧЕНИЕ ХРОМА ИЗ ГАЛЬВАНИЧЕСКИХ РАСТВОРОВ [c.334]
Проводятся обширные исследования по изучению процесса осаждения хрома и растворов на основе хлорида трехвалентного хрома, которые обеспечивают более высокие эффективность катода и скорость осаждения в сочетании с более низкими рабочими температурами. Гальванические покрытия хромом, образующиеся в ваннах трехвалентного хрома, немного темнее покрытий, получаемых в ваннах из растворов шестивалентных ионов хрома в присутствии серной кислоты. [c.92]
Спаивание со сталью несколько затруднено ввиду ее легкой окисляемости при нагревании и высокого значения коэффициента теплового расширения 151-70 К (в интервале температур 20— 300 °С) . Окислы стали довольно трудно растворяются в стекле, что препятствует получению вакуумного спая. Адгезионные свойства стекла к стали можно улучшить разными способами применить гальваническое покрытие стали медью (толщиной около 3 мкм), хромирование поверхности стали путем нанесения хрома гальванически или из газовой фазы (окислы хрома хорошо смачиваются стеклом), а также эмалевое покрытие с добавками закиси никеля или окиси кобальта в количестве 1 вес.%- [c.155]
Гальванический элемент, образовавшийся при коррозии в кислой среде хрома, спаянного с никелем, дает ток 5А. Какой объем (н. у.) водорода выделился за 30 с работы этого элемента Какая, масса хрома растворилась [c.154]
В ходе эксплуатации гальванических производств металлообрабатывающих предприятий образуется два вида отходов промышленные сточные воды и отработанные гальванические растворы, в которых содержатся токсичные примеси тяжелых металлов (хром, никель, цинк, кадмий), цианистые соединения, фенолы и т.д. Регенерация гальванических растворов для повторного использования сложная, дорогостоящая и не всегда осуществимая мера. Поэтому в большинстве случаев их направляют на очистные сооружения для обезвреживания. [c.119]
В настоящее время большое распространение получают физико-химические методы очистки сточных вод, благодаря которым в производство возвращают не только очищенную воду, но и ценные металлы. Для очистки сточных вод с общим со-лесодержанием до 2—3 г/л рекомендуют применять в основном метод ионного обмена, который обладает универсальностью и позволяет удалять тяжелые металлы не только в виде катионов, но и анионов. Другим перспективным методом очистки -сточных вод является метод обратного осмоса. Современные высокоселективные обратноосмотические мембраны делают метод весьма эффективным и экономичным. Электрохимический способ наиболее часто применяется для удаления шестивалентного хрома из сточных вод. Способ заключается в восстановлении Сг +—>-Сг + с помощью ионов двухвалентного железа и осаждении Сг(ОН)з. Применяют также электрохимические методы очистки цианидсодержащей сточной воды, заключающийся в окислении цианидов на графитовых анодах, а также извлечения ионов тяжелых металлов (иногда селективно на вращающихся катодах при заданных потенциалах осаждения). Электрохимический способ очистки более экономичен для растворов, содержащих более чем 0,1 г/л металлов. Для очистки сточных вод гальванических производств используют также процессы электрокоагуляции. При этом применяют электролизеры с анодами из низкоуглеродистых сталей, которые растворяются в про- [c.350]
Молибден широко применяется в вакуумной технике. Он по химическим свойствам является аналогом хрома. Гальванической обработке подвергается с целью повышения его жаростойкости, возможности пайки и для других специальных целей. Ниже приводится схема технологического процесса осаждения металлов на молибден. Обезжиривание в 10—20%-ном растворе едкого натра пр,и температуре до 60° С. Катодная плотность тока до 8 а/дм , продолжительность 5—10 мин., промывка в воде, декапирование в соляной кислоте (уд. вес. 1,19) в течение до [c.205]
Извлечение хрома из гальванических растворов 335 [c.335]
К наиболее токсичным веществам, используемым в гальванических производствах, относятся свинец, хром, ртуть, мышьяк и их соли, цианиды. С целью обеспечения безопасных условий труда все работающие в цехе должны четко выполнять инструкции и правила эксплуатации оборудования, а также правила обращения с ядовитыми вешествами и растворами. При работе с цианидными электролитами ванны должны быть оснащены мощной бортовой вентиляцией. Кроме того, должны соблюдаться требования к параметрам воздушной среды па ГОСТ 12.1.003—76. [c.351]
Применяемая с 60-х гг. 20 в. технология Инметко отличается чрезвычайным разнообразием компонентов исходного сырья пыли и шламы доменного, конвертерного и электросталеплавильного переделов, аглофабрики, прокатная окалина, шлифовальная пыль, пыль мешочных фильтров, отработанные травильные растворы, фильтраты с никелем и хромом гальванических участков, отработанные хромитовые и углеродистые огнеупоры из травильных ванн, использованные катализаторы и батарейки. [c.75]
Металлический хром получен Девиллем (вероятно, с содержанием углерода) при восстановлении углем окиси хрома при температуре, близкой к плавлению платины имеет стальной цвет, уд. вес 5,9 и весьма большую твердость (хорошо полируется), растворяется в соляной кислоте, но холодная разведенная серная и азотная кислоты на него не действуют. Бунзен получил металлический хром, разлагая раствор Сг2С1 гальваническим током, в виде чешуек серого цвета (уд. вес 7,3). Вёлер получил кристаллический хром, накаливая смесь безводного Сг С с измельченным цинком и хлористым калием до температуры кипения цинка. После охлаждения цинк растворяется в разбавленной азотной кислоте, причем остается серый кристаллический хром (уд. вес 6,81). Фреми приготовил также кристаллический хром, действуя парами натрия на безводный Сг С1 в струе водорода кристаллы металлического хрома имели черный цвет, кубическую форму, значительную твердость и сопротивлялись действию кислот. Глат-цель (1890) получил кристаллический порошок Сг при накаливании двойной соли КСгС1 с магнием, уд. веса 6,7 такой хром в кислотах легко растворялся с выделением водорода. Таким образом, повидимому, является явное разноречие между показаниями разных исследователей, что объяснилось, как указано далее, только в недавнее время. Муассан (1893), при [c.238]
Осаждение хрома производится на практике из электролита, содержащего в качестве основного компонента не соль хрома, как в большинстве гальванических процессов, а хромовый ангидрид. Водный раствор хромового ангидрида представляет смесь поли-хромовых кислот, Б основном Н2СГО4 и Н2СГ2О7, которые находятся в подвижном равновесии [c.191]
Уже предварительное рассмотрение такой схемы регенерации ценных компонентов из гальванических шламов позволяет выявить ее существенные недостатки сложность аппаратного оформления процесса, многостадийность, наличие токсичных органических реагентов. Кроме того, организация такого процесса требует серьезных капитальных вложений. При внедрении процесса открытым остается вопрос об использовании твердых компонентов после фильтрации раствора выщелачивания щламов, а также окончательного обезвреживания жидкой фазы после от-фильтровывания осадка гидроокиси хрома. [c.104]
На Палемонском керамическом заводе (Литовская ССР) эти шламы с 1983 г применяют при производстве глиняной черепицы. Для этого специально оборудован участок приема отходов. Гальванические отходы загружают в контейнеры вместимостью 2 т и централизованно доставляют на завод. Выгрузка контейнеров механизирована. После выгрузки отходов контейнеры и помещение промывают водой, которая стекает в резервуары с отходами. Количество шлама в глиняной смеси 5 % (об.). Подготовка сырьевой смеси шликерная. Формовка изделий пластическая, с предварительной сушкой шликерной шихты во вращающейся сушилке при 600—700 °С. За год принимается 1200 т гальванических отходов. Исследование образцов черепицы, полученных в промышленных условиях, показало, что при повышении температуры начинаются реакции между твердыми веществами и образуются кристаллические силикаты и стекло [45]. При 950 °С часть Na, Са, Zn, d, Ni, Си находятся в форме силикатов, а другая часть растворяется в стеклообразных сплавах. Силикат Сг (III) не образовывается. После прокаливания при 950 °С оксид Сг становится устойчивым, поэтому особое внимание было уделено созданию условий, при которых Сг (III) не переходит в Сг (VI). Оказалось, что ионы Fe , которыми обогащается осадок при очистке сточных вод, предотвращают переход хрома в шестивалентную форму. Кроме того, на определенной стадии создается восстановительная атмосфера в печи. [c.211]
Металлические матрицы перед гальваническим процессом также очищают кроме того, для облегчения отделения гальванокопин от матрицы на нее наносят очень тонкий (1—2 мкм) промежуточный слой никеля или серебра, который легко химически оксидируется. Затем матрицу помещают В гальваническую ванну и получают с нее точную пустотелую копию ИЗДелия. При СЛОЖНЫХ формах изделий (бюсты, статуи) их делят НЗ дзс И дзжб три части, ДЛЯ каждой из которых изготавливают свою матрицу и копию. Затем отдельные копии соединяют друг с другом пайкой. Широкое применение получила гальванопластика в полиграфии. Свинцовую пластину накладывают на цинковое или медное клише, предварительно смазав керосином или раствором воска в бензине, после чего прессуют оттиск под давлением 50—100 МПа. Полученную матрицу отделяют от оригинала и помещают в гальванопластическую ванну, где снимают копии с клише из меди, а затем методами гальваностегии покрывают их тонким слоем никеля, железа или хрома. Если цинковое клише выдерживает 25—30 тыс. оттисков, а медные копии — до 200— 250 тыс., то покрытые никелем или железом — до миллиона оттисков, а хромированные — до полутора миллионов оттисков, [c.347]
Кроме того, следует учитывать, что толщина осадка зависит от расстояния между анодом и катодом. Способность раствора электролита при нанесении гальванических покрытий преодолевать эту зависимость называют его рассеивающей способностью (или, правильнее, его макрорассеивающей способностью). Медь — металл с высокой рассеивающей способностью, хром — металл с плохой рассеивающей способностью. На это свойство может влиять также состав ванны и режим ее работы. Из-за [c.87]
Электроосаждение хрома почти всегда производят из растворов серной или хромовой кислот с использованием анодов из свинца. Рабочая температура меняется в пределах 37—65° С в зависимости от используемого электролита для нанесения гальванических покрытий. Хром периодически пополняют, заменяя использованный, за счет добавок хромовой кислоты. Покрытия блестящие, но рассеивающая способность слабая, что приводит к неравномерности покрытия по толщине и неполному заполнению углублений обрабатываемых изделий. Кроме того, КПД катода низкий (в пределах 8—18% в зависимости от используемого раствора и рабочих условий). Более высокий КПД катода можно получить в ваннах, катализуемых фторидом кремния (до 25%), или в ваннах (типа Борнхаузера) тетрахромата (до 30%). [c.92]
В сильноокислительных средах никель и его сплавы пассивируются и показывают высокую стойкость. Никель устойчив в щелочах всех концентраций и температур, в растворах многих солей, в атмосфере и в природных водах. Наибольшее применение никель находит в качестве гальванических покрытий. Промышленными сплавами никеля являются сплавы с медью, молибденом и хромом. [c.76]
chem21.info